Mastering CAD Technology: Advanced Techniques for Modern Mechanical Design
Md Anamul Hasan
8 min read
CADSolidWorksCATIADesign AutomationAI DesignSimulationProductivityEngineering Software

# Mastering CAD Technology: Advanced Techniques for Modern Mechanical Design
Computer-Aided Design (CAD) technology has undergone a revolutionary transformation over the past decade, evolving from basic drafting tools to sophisticated design ecosystems that integrate artificial intelligence, real-time simulation, and advanced manufacturing capabilities. As a mechanical engineer with over 8 years of hands-on experience across multiple CAD platforms, I've witnessed firsthand how these technologies are reshaping the engineering landscape and creating unprecedented opportunities for innovation.
## The Revolutionary CAD Ecosystem of Today
Modern CAD platforms have transcended traditional boundaries, offering integrated solutions that fundamentally change how we approach mechanical design:
### **Next-Generation Parametric Modeling**
Today's parametric modeling capabilities extend far beyond simple dimension-driven features. Advanced platforms now offer:
- **Intelligent feature recognition** that automatically identifies and categorizes geometric patterns
- **Contextual design suggestions** based on engineering best practices and industry standards
- **Multi-physics parameter linking** that connects mechanical, thermal, and electrical properties
- **Adaptive modeling** that automatically adjusts designs based on changing requirements
### **Real-Time Simulation Integration**
The integration of simulation capabilities directly into the CAD environment has eliminated the traditional design-simulate-redesign cycle:
- **Live FEA analysis** that updates automatically as geometry changes
- **Integrated CFD visualization** for immediate fluid flow feedback
- **Thermal analysis** with real-time temperature distribution mapping
- **Dynamic motion simulation** for mechanism validation during design
### **AI-Powered Generative Design**
Artificial intelligence has introduced revolutionary capabilities that push the boundaries of traditional design thinking:
- **Topology optimization** that creates organic, material-efficient structures
- **Multi-objective optimization** balancing performance, weight, and cost simultaneously
- **Design space exploration** that generates hundreds of viable alternatives
- **Machine learning-based design validation** that predicts performance before simulation
### **Cloud-Native Collaboration Platforms**
Modern CAD workflows have embraced cloud technologies to enable unprecedented collaboration:
- **Real-time collaborative modeling** with multiple engineers working simultaneously
- **Automated version control** that eliminates design conflicts
- **Global accessibility** from any device, anywhere in the world
- **Integrated project management** with timeline and milestone tracking
## Advanced Techniques That Transform Engineering Productivity
### **1. Intelligent Design Automation**
In my recent work implementing design automation across multiple projects, I've discovered techniques that go far beyond basic macro programming:
**Template-Based Design Systems**: I developed a comprehensive library of parametric templates for HVAC components that reduced initial design time by 65%. These templates include:
- Intelligent sizing algorithms based on performance requirements
- Automated material selection based on environmental conditions
- Built-in compliance checking for industry standards (ASHRAE, ASME)
- Integrated cost estimation and optimization
**Advanced Macro Programming**: Utilizing Visual Basic and Python integration within CAD platforms, I created sophisticated automation tools that:
- Generate complete assemblies from performance specifications
- Automatically update drawings and documentation when designs change
- Perform batch processing of design variations for optimization studies
- Interface with external databases for material properties and standards
### **2. Simulation-Driven Design Methodology**
The integration of simulation directly into the design process has fundamentally changed my approach to mechanical engineering:
**Concurrent Engineering Workflow**: By embedding FEA and CFD analysis throughout the design process, I've achieved:
- 40% reduction in design iteration cycles
- 25% improvement in first-time-right design success
- Elimination of late-stage design changes that traditionally cost 10x more to implement
**Multi-Physics Optimization**: Recent projects have leveraged coupled simulation capabilities:
- **HVAC System Design**: Simultaneous thermal and fluid analysis optimized energy efficiency by 35%
- **Electric Vehicle Battery Housing**: Coupled thermal-structural analysis achieved 20% weight reduction while improving safety performance
- **Precision Manufacturing Tooling**: Vibration and thermal analysis reduced machining tolerances by 30%
### **3. Data-Driven Design Decision Making**
Modern CAD platforms generate enormous amounts of design data that can be leveraged for intelligent decision-making:
**Performance Database Integration**: I've developed systems that:
- Track design performance across multiple projects
- Identify optimal design patterns based on historical success
- Automatically flag designs that deviate from proven best practices
- Generate performance predictions based on similarity analysis
**Real-Time Cost Analysis**: Integration with manufacturing cost databases enables:
- Instant cost feedback during design modifications
- Material optimization based on real-time pricing
- Manufacturing process selection based on quantity and timeline requirements
- Total cost of ownership calculations including maintenance and lifecycle costs
## Cutting-Edge CAD Platforms and Capabilities
### **SolidWorks 2024+: Enhanced Productivity Features**
Recent SolidWorks updates have introduced game-changing capabilities:
**3DExperience Platform Integration**: Cloud-based collaboration with real-time synchronization across global teams. In a recent international project, this enabled seamless coordination between teams in Toronto, Munich, and Tokyo.
**Advanced Surfacing Tools**: Complex surface modeling capabilities that rival dedicated Class-A surfacing software, particularly valuable for automotive and consumer product applications.
**Integrated Simulation Ecosystem**: Direct integration with ANSYS and other simulation packages eliminates data translation errors and reduces simulation setup time by 50%.
### **CATIA V6/3DExperience: Systems Engineering Excellence**
For complex, multi-disciplinary projects, CATIA's systems engineering approach provides:
**Systems Architecture Modeling**: Capability to model complete product systems including mechanical, electrical, and software components in a unified environment.
**Advanced Manufacturing Integration**: Direct connection to manufacturing planning and robotics programming, enabling true digital twin implementations.
**Collaborative Space Management**: Project spaces that enable controlled collaboration with suppliers and customers while protecting intellectual property.
### **Fusion 360: Cloud-Native Innovation**
Autodesk's cloud-first approach offers unique advantages:
**Generative Design Leadership**: Most advanced AI-powered design generation capabilities, creating designs that human engineers might never consider.
**Integrated CAM and Simulation**: Seamless workflow from design through manufacturing with automatic tool path generation and optimization.
**Unlimited Cloud Computing**: Access to virtually unlimited computational resources for complex simulations and optimization studies.
## Real-World Implementation: Case Studies from Practice
### **Case Study 1: Next-Generation HVAC System Design**
**Challenge**: Design an energy-efficient HVAC system for a 250,000 sq ft commercial complex with strict energy performance requirements.
**Advanced CAD Solution**:
- Used integrated CFD analysis to optimize ductwork geometry in real-time
- Implemented generative design for custom diffuser components
- Leveraged cloud-based collaboration for coordination with electrical and plumbing teams
- Automated energy modeling integration for LEED compliance verification
**Results**:
- 35% energy consumption reduction compared to baseline design
- 50% reduction in design development time
- Zero design conflicts during construction
- LEED Platinum certification achieved
### **Case Study 2: Precision Manufacturing Tooling Optimization**
**Challenge**: Develop custom tooling for automotive component manufacturing with aggressive cost and precision targets.
**Advanced CAD Solution**:
- Utilized topology optimization for weight reduction while maintaining stiffness
- Implemented automated tolerance stack-up analysis
- Integrated manufacturing simulation for process validation
- Created parametric tooling families for scalability
**Results**:
- 28% reduction in tooling weight
- 15% improvement in manufacturing precision
- 40% reduction in tooling development time
- 25% cost savings through material optimization
### **Case Study 3: Electric Vehicle Component Development**
**Challenge**: Design battery housing that maximizes safety while minimizing weight and cost.
**Advanced CAD Solution**:
- Multi-physics simulation combining thermal, structural, and crash analysis
- Generative design exploration of internal reinforcement structures
- Automated material selection based on performance and cost criteria
- Real-time collaboration with safety testing teams
**Results**:
- 20% weight reduction while exceeding safety requirements
- 15% cost reduction through material optimization
- Accelerated testing phase due to accurate simulation predictions
- Patent-pending innovative structural design features
## Emerging Technologies Shaping the Future
### **Artificial Intelligence Integration**
The next generation of CAD platforms will feature deeper AI integration:
**Intelligent Design Assistants**: AI systems that understand design intent and proactively suggest improvements, identify potential issues, and recommend optimization strategies.
**Automated Design Generation**: Complete design automation based on performance requirements, with AI generating multiple viable solutions for engineer evaluation.
**Predictive Maintenance Design**: AI-driven design features that optimize products for maintainability and predict failure modes during the design phase.
### **Virtual and Augmented Reality Integration**
Immersive technologies are beginning to transform the design experience:
**VR Design Environments**: Three-dimensional design spaces where engineers can manipulate models using natural hand gestures and movements.
**AR Assembly Planning**: Overlay of digital designs onto physical environments for installation and maintenance planning.
**Mixed Reality Collaboration**: Virtual meetings where remote participants can interact with 3D models as if they were physically present.
### **Quantum Computing Applications**
While still emerging, quantum computing promises to revolutionize simulation capabilities:
**Complex Optimization Problems**: Quantum algorithms capable of solving optimization problems that are intractable with classical computers.
**Advanced Material Simulation**: Quantum simulation of material properties at the molecular level for unprecedented accuracy.
**Global Optimization**: Ability to find true global optima for complex multi-variable design problems.
## Best Practices for CAD Excellence in Modern Engineering
### **1. Strategic Implementation Framework**
**Technology Roadmap Development**: Create a 3-5 year plan for CAD technology adoption that aligns with business objectives and project requirements.
**Training and Skill Development**: Invest in continuous learning programs that keep teams current with emerging capabilities. In my experience, teams that receive regular advanced training are 40% more productive.
**Change Management**: Implement structured approaches to technology adoption that minimize disruption while maximizing benefits.
### **2. Quality and Standards Management**
**Design Standard Development**: Establish comprehensive design standards that leverage advanced CAD capabilities while ensuring consistency across projects.
**Model Quality Assurance**: Implement automated model checking and validation procedures that catch errors before they propagate through the design process.
**Documentation Integration**: Ensure that advanced CAD capabilities are properly documented and integrated into standard operating procedures.
### **3. Performance Optimization**
**Hardware Infrastructure**: Invest in workstation and network infrastructure that can fully leverage advanced CAD capabilities.
**Software Integration**: Develop integrated workflows that eliminate data translation and reduce manual intervention.
**Performance Monitoring**: Track and optimize CAD system performance to ensure maximum productivity from advanced features.
## Strategic Career Development in Advanced CAD
For mechanical engineers looking to advance their careers, mastering advanced CAD technologies is essential:
### **Skill Development Priorities**
1. **Multi-Platform Proficiency**: Develop expertise across multiple CAD platforms to increase versatility
2. **Simulation Integration**: Master integrated simulation workflows for competitive advantage
3. **Automation Programming**: Learn scripting and automation to increase productivity
4. **Cloud Collaboration**: Develop skills in distributed design workflows
5. **AI/ML Understanding**: Gain familiarity with AI-powered design tools and methodologies
### **Professional Certification Strategy**
- **Platform-Specific Certifications**: Pursue advanced certifications in primary CAD platforms
- **Simulation Expertise**: Obtain specialized certifications in FEA, CFD, and multi-physics simulation
- **Industry Standards**: Develop expertise in relevant industry standards and compliance requirements
## Conclusion: Embracing the CAD Revolution
The transformation of CAD technology represents one of the most significant advances in mechanical engineering in the past century. Engineers who embrace these advanced capabilities and develop expertise in emerging technologies will have unprecedented opportunities to create innovative solutions and advance their careers.
The key to success lies not just in learning new software features, but in fundamentally reimagining how we approach the design process. By integrating AI-powered optimization, real-time simulation, and collaborative workflows, we can achieve levels of innovation and efficiency that were previously impossible.
As we look toward the future, the continued convergence of AI, cloud computing, and immersive technologies promises even more revolutionary changes. The engineers who begin mastering these technologies today will be the leaders of tomorrow's engineering innovations.
**What advanced CAD techniques have transformed your engineering practice? I'm always eager to learn about new approaches and share experiences with fellow engineers working at the cutting edge of design technology.**
---
*Interested in diving deeper into advanced CAD techniques? Check out my other articles on [Sustainable Engineering Practices](/blog/sustainable-engineering-practices) and explore my [portfolio of innovative engineering projects](/portfolio) showcasing these technologies in action.*
About the Author
Related Articles
You Might Also Like
Continue exploring with these hand-picked articles related to your interests.
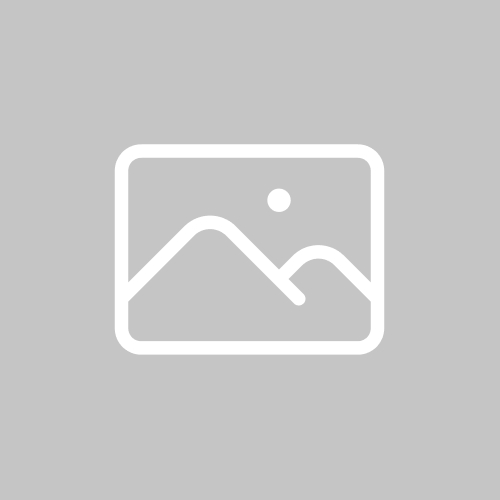
8 min read
The Future of Mechanical Engineering in Sustainable Design
Exploring how mechanical engineers are leading the transformation toward sustainable solutions while maintaining performance excellence and driving innovation in design practices.
Sustainable EngineeringGreen DesignClimate Solutions +2
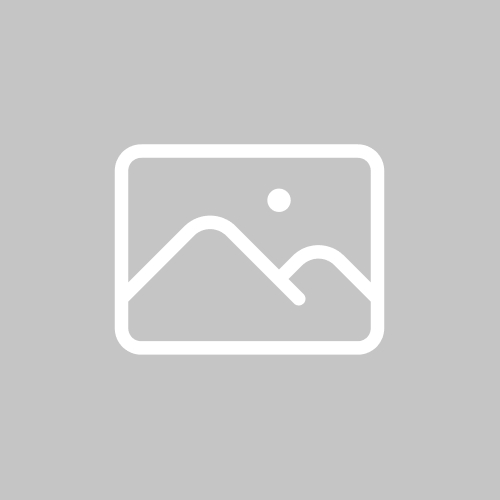
12 min read
Material Selection Mastery: A Strategic Guide for Mechanical Engineers
A comprehensive guide to strategic material selection methodologies, advanced materials science, and decision-making frameworks for optimizing performance, cost, and sustainability in mechanical engineering applications.
Materials ScienceMaterial SelectionManufacturing +4
Looking for more insights?