Material Selection Mastery: A Strategic Guide for Mechanical Engineers
Md Anamul Hasan
12 min read
Materials ScienceMaterial SelectionManufacturingDesign OptimizationCost EngineeringSustainabilityAdvanced Materials
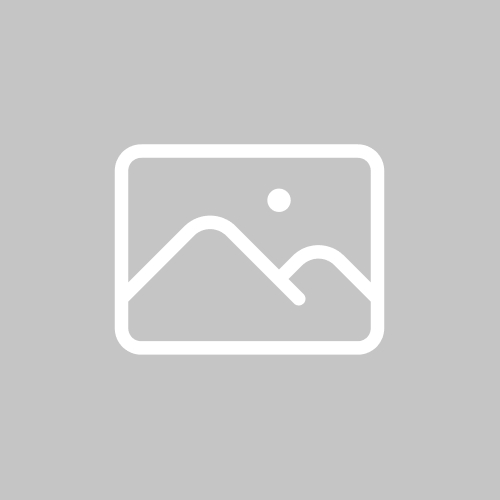
# Material Selection Mastery: A Strategic Guide for Mechanical Engineers
Material selection represents one of the most critical and complex decisions in mechanical engineering design, fundamentally determining project success across performance, cost, sustainability, and manufacturing considerations. After 8+ years of navigating diverse material challenges across industries from aerospace to renewable energy, I've developed a comprehensive framework for strategic material selection that consistently delivers optimal outcomes.
The consequences of material selection extend far beyond initial cost considerations. A well-chosen material can enable breakthrough performance, reduce lifecycle costs by 30-50%, and create competitive advantages that last for years. Conversely, poor material choices can lead to catastrophic failures, costly redesigns, and missed market opportunities.
## Fundamental Material Science for Strategic Decision-Making
### **Advanced Mechanical Properties Analysis**
Understanding material behavior under real-world conditions requires deep analysis of mechanical properties and their interactions:
**Strength Characteristics and Design Margins**:
Modern engineering demands understanding strength beyond simple tensile values. In my recent work on precision manufacturing equipment, I analyzed:
- **Multiaxial stress states**: Real components rarely experience simple tension; combined loading requires von Mises stress analysis
- **Temperature-dependent strength**: Strength degradation with temperature can be dramatic; titanium alloys lose 50% strength at 500°C
- **Strain rate sensitivity**: Impact loading can double apparent strength in some materials while making others brittle
- **Fatigue life prediction**: S-N curves must be understood for finite-life design, especially for rotating machinery
**Fracture Mechanics and Damage Tolerance**:
Critical for safety-critical applications where failure consequences are severe:
- **Fracture toughness (KIC)**: Determines resistance to crack propagation; essential for pressure vessels and structural components
- **Fatigue crack growth rates**: Da/dN curves predict remaining life with existing damage
- **Damage tolerance design**: Accept that flaws exist and design for safe crack growth rates
- **Non-destructive testing requirements**: Inspection intervals based on crack growth predictions
**Viscoelastic Behavior in Polymers**:
Time-dependent behavior affects long-term performance:
- **Creep resistance**: Long-term loading causes permanent deformation; crucial for structural polymers
- **Stress relaxation**: Maintained strain leads to stress reduction; affects bolt preload and gasket performance
- **Temperature transitions**: Glass transition affects mechanical properties dramatically
- **Environmental stress cracking**: Combined stress and chemical exposure can cause premature failure
### **Thermal and Environmental Performance**
Real-world applications involve complex environmental conditions requiring comprehensive analysis:
**Thermal Management Considerations**:
- **Thermal expansion mismatch**: Different materials expand at different rates, causing interface stresses
- **Thermal cycling fatigue**: Repeated heating and cooling causes crack initiation and growth
- **Thermal shock resistance**: Rapid temperature changes can cause catastrophic failure
- **Heat treatment effects**: Processing temperatures affect microstructure and properties
**Environmental Degradation Mechanisms**:
- **Corrosion kinetics**: Understanding reaction rates enables lifetime prediction
- **UV degradation**: Polymer chain scission reduces mechanical properties over time
- **Oxidation resistance**: High-temperature exposure causes material degradation
- **Chemical compatibility**: Swelling, dissolution, or chemical attack can compromise integrity
## Advanced Material Categories and Strategic Applications
### **High-Performance Metallic Systems**
**Superalloys for Extreme Environments**:
In my work on industrial gas turbine components, superalloys provided exceptional performance:
- **Nickel-based superalloys (Inconel 718, Waspaloy)**: Maintain strength at 700°C+, resist oxidation and creep
- **Cobalt-based alloys (Stellite)**: Superior wear resistance and high-temperature strength
- **Iron-based superalloys (A-286)**: Cost-effective alternative with good high-temperature properties
- **Single-crystal alloys**: Eliminate grain boundaries for ultimate high-temperature performance
**Advanced Aluminum Systems**:
Beyond conventional alloys, advanced aluminum systems offer unique advantages:
- **Aluminum-lithium alloys**: 10% density reduction with improved stiffness for aerospace
- **Metal matrix composites (Al/SiC)**: Combine aluminum ductility with ceramic reinforcement
- **Foam structures**: Ultra-lightweight with excellent energy absorption
- **Powder metallurgy alloys**: Achieve compositions impossible with conventional casting
**Titanium Alloy Optimization**:
Titanium's exceptional properties justify higher costs in demanding applications:
- **Alpha alloys (Ti-5Al-2.5Sn)**: Excellent weldability and corrosion resistance
- **Beta alloys (Ti-15V-3Cr-3Al-3Sn)**: High strength and spring properties
- **Alpha-beta alloys (Ti-6Al-4V)**: Balanced properties for general aerospace use
- **Near-alpha alloys**: Optimized for high-temperature applications
### **Revolutionary Polymer and Composite Systems**
**High-Performance Thermoplastics**:
Modern engineering plastics rival metals in many applications:
- **PEEK (Polyetheretherketone)**: Exceptional chemical resistance and high-temperature performance to 260°C
- **PPS (Polyphenylene sulfide)**: Outstanding dimensional stability and flame resistance
- **LCP (Liquid crystal polymers)**: Ultra-low thermal expansion and exceptional strength
- **PAI (Polyamide-imide)**: Combines polyimide thermal stability with processability
**Advanced Composite Architectures**:
Beyond simple laminates, advanced composites offer tailored properties:
- **3D woven fabrics**: Through-thickness reinforcement prevents delamination
- **Hybrid composites**: Combine different fiber types for optimized properties
- **Thermoplastic composites**: Unlimited shelf life and recyclability
- **Bio-composites**: Natural fibers provide sustainability with adequate performance
**Nanocomposite Technologies**:
Nanoscale reinforcement enables property enhancement with minimal weight impact:
- **Carbon nanotube reinforcement**: Electrical conductivity and strength enhancement
- **Graphene integration**: Thermal conductivity and barrier properties
- **Clay nanocomposites**: Improved barrier properties and flame resistance
- **Nanocellulose**: Renewable reinforcement with excellent mechanical properties
### **Emerging Smart and Functional Materials**
**Shape Memory Alloys (SMAs)**:
Enable innovative design solutions through programmable shape changes:
- **Nitinol (NiTi)**: Biocompatible with excellent shape memory and superelasticity
- **Copper-based SMAs**: Cost-effective for less demanding applications
- **Ferromagnetic SMAs**: Magnetic activation enables wireless control
- **Polymer SMAs**: Lower activation temperatures and easier processing
**Magnetorheological Materials**:
Variable properties enable adaptive systems:
- **MR fluids**: Variable damping for shock absorbers and clutches
- **MR elastomers**: Tunable stiffness for vibration control
- **Electromagnetic compatibility**: Shielding effectiveness varies with activation
## Strategic Selection Methodology: A Systems Approach
### **Requirements Definition and Analysis**
My systematic approach begins with comprehensive requirements analysis:
**Performance Requirements Matrix**:
- **Primary functions**: Load bearing, thermal management, electrical properties
- **Secondary functions**: Corrosion resistance, appearance, regulatory compliance
- **Failure consequences**: Safety-critical vs. non-critical failure modes
- **Service environment**: Temperature, humidity, chemical exposure, UV radiation
- **Loading conditions**: Static, dynamic, cyclic, impact, creep
**Manufacturing Constraints Analysis**:
- **Processing capabilities**: Available equipment and expertise
- **Joining requirements**: Welding, bonding, mechanical fastening compatibility
- **Machining considerations**: Tool wear, surface finish, dimensional tolerances
- **Quality control**: Inspection methods and acceptance criteria
- **Supply chain**: Material availability, lead times, supplier reliability
**Economic Optimization Framework**:
- **Total cost of ownership**: Material, processing, quality, maintenance, disposal
- **Value engineering opportunities**: Function/cost optimization
- **Risk-cost analysis**: Probability and impact of material-related failures
- **Sensitivity analysis**: How cost varies with property requirements
### **Advanced Selection Tools and Techniques**
**Multi-Criteria Decision Analysis (MCDA)**:
Systematic evaluation of complex trade-offs:
1. **Criteria weighting**: Assign relative importance to different requirements
2. **Performance scoring**: Quantify how well each material meets criteria
3. **Sensitivity analysis**: Understand how weight changes affect selection
4. **Risk assessment**: Consider uncertainty in material properties and costs
**Materials Informatics and AI**:
Leverage data science for intelligent selection:
- **Property prediction models**: Machine learning for property estimation
- **Materials databases**: CES EduPack, GRANTA, MatWeb for comprehensive data
- **Optimization algorithms**: Genetic algorithms for multi-objective optimization
- **Performance prediction**: Finite element analysis with material models
### **Real-World Case Studies: Strategic Selection in Action**
**Case Study 1: Next-Generation HVAC Heat Exchanger**
**Challenge**: Design heat exchanger for commercial building application requiring 25-year service life in coastal environment with 40% efficiency improvement over existing designs.
**Strategic Analysis**:
- **Environmental factors**: Salt air corrosion, temperature cycling, potential freeze-thaw
- **Performance requirements**: Thermal conductivity, corrosion resistance, formability
- **Economic constraints**: Cost target 20% above current design
- **Manufacturing considerations**: Available fabrication methods, joining techniques
**Material Selection Process**:
1. **Initial screening**: Eliminated carbon steel due to corrosion issues
2. **Detailed analysis**: Compared stainless steel 316L, aluminum 3003, and copper-nickel alloy
3. **Life cycle costing**: Included maintenance, replacement, and energy costs
4. **Prototype testing**: Accelerated corrosion and thermal cycling tests
**Optimal Solution**: Aluminum 3003 with specialized coating system
- **Performance**: 42% efficiency improvement through enhanced heat transfer
- **Durability**: Projected 30-year service life based on testing
- **Cost**: 15% premium over target but 35% total cost of ownership reduction
- **Sustainability**: 95% recyclable with 30% lower carbon footprint
**Case Study 2: Precision Manufacturing Tooling Optimization**
**Challenge**: Develop custom tooling for automotive stamping operation with aggressive productivity targets and precision requirements.
**Strategic Analysis**:
- **Wear resistance**: 500,000+ cycle life requirement
- **Dimensional stability**: ±0.025mm tolerance maintenance
- **Thermal management**: Heat generation during high-speed operation
- **Manufacturing**: Complex geometry requiring EDM machining
**Material Selection Process**:
1. **Tool steel evaluation**: Compared D2, A2, S7, and powder metallurgy grades
2. **Surface treatment options**: Analyzed coatings and heat treatments
3. **Thermal modeling**: FEA to predict temperature distribution and distortion
4. **Wear testing**: Laboratory simulation of service conditions
**Optimal Solution**: Powder metallurgy tool steel with DLC coating
- **Performance**: 40% longer tool life than conventional D2
- **Precision**: Maintained tolerances through full service life
- **Productivity**: 25% faster cycle times due to improved heat dissipation
- **Cost-effectiveness**: 60% lower cost per part despite higher initial investment
**Case Study 3: Sustainable Product Redesign Initiative**
**Challenge**: Redesign consumer appliance component to achieve 50% carbon footprint reduction while maintaining performance and cost competitiveness.
**Strategic Analysis**:
- **Sustainability metrics**: Life cycle assessment including end-of-life
- **Performance requirements**: Mechanical strength, dimensional stability, appearance
- **Manufacturing constraints**: Existing injection molding equipment
- **Market requirements**: Cost parity with existing design
**Material Selection Process**:
1. **Bio-based alternatives**: Evaluated PLA, PHA, bio-based PA
2. **Recycled content**: Analyzed post-consumer and post-industrial options
3. **Hybrid approaches**: Combined materials for optimized properties
4. **Life cycle modeling**: Cradle-to-grave environmental impact analysis
**Optimal Solution**: Bio-based PA11 with glass fiber reinforcement
- **Sustainability**: 52% carbon footprint reduction achieved
- **Performance**: Superior impact resistance and dimensional stability
- **Economics**: Cost-neutral through process optimization
- **Market acceptance**: Excellent consumer response to sustainability story
## Advanced Cost Optimization Strategies
### **Value Engineering Methodologies**
**Function-Based Material Selection**:
Optimize material choice based on required functions rather than traditional approaches:
- **Primary function analysis**: Identify minimum property requirements for core function
- **Secondary function optimization**: Balance supporting requirements against cost
- **Over-specification elimination**: Avoid unnecessary property margins that increase cost
- **Hybrid design strategies**: Use premium materials only where maximum performance is required
**Total Cost of Ownership Modeling**:
Comprehensive cost analysis includes all lifecycle phases:
- **Acquisition costs**: Material, processing, quality control, inventory
- **Operating costs**: Energy consumption, maintenance, replacement
- **End-of-life costs**: Disposal, recycling, environmental compliance
- **Risk costs**: Probability-weighted failure consequences
**Supply Chain Optimization**:
Strategic supplier relationships and sourcing decisions:
- **Supplier qualification**: Technical capability, quality systems, financial stability
- **Geographic considerations**: Transportation costs, lead times, trade regulations
- **Volume negotiations**: Price breaks, exclusive agreements, long-term contracts
- **Dual sourcing**: Balance cost optimization with supply security
### **Sustainability Integration Framework**
**Life Cycle Assessment (LCA) Integration**:
Systematic environmental impact evaluation:
- **Impact categories**: Climate change, resource depletion, toxicity, eutrophication
- **System boundaries**: Cradle-to-grave vs. cradle-to-gate analysis
- **Allocation methods**: How to distribute impacts across co-products
- **Uncertainty analysis**: Understanding confidence intervals in results
**Circular Economy Design Principles**:
Material selection supporting circular economy goals:
- **Design for disassembly**: Material compatibility with separation processes
- **Material identification**: Marking systems for end-of-life sorting
- **Recycled content integration**: Balancing performance with sustainability goals
- **Biodegradability requirements**: Appropriate end-of-life scenarios
**Regulatory Compliance and Future-Proofing**:
Anticipating regulatory changes and market trends:
- **RoHS and REACH compliance**: Restricted substances and registration requirements
- **Carbon pricing impacts**: How carbon costs affect material economics
- **Extended producer responsibility**: Manufacturer responsibility for end-of-life
- **Industry sustainability standards**: Sector-specific environmental requirements
## Future Trends and Emerging Technologies
### **Next-Generation Material Technologies**
**AI-Designed Materials**:
Machine learning accelerates material discovery and optimization:
- **Property prediction models**: Faster screening of material candidates
- **Inverse design**: Design materials with specific target properties
- **High-throughput experimentation**: Automated synthesis and testing
- **Materials genome initiative**: Systematic mapping of structure-property relationships
**Additive Manufacturing Materials**:
3D printing enables new material possibilities:
- **Multi-material printing**: Gradient properties and functional integration
- **Metal AM alloys**: Specialized compositions for powder bed fusion
- **Polymer AM materials**: High-performance thermoplastics and thermosets
- **Composite AM**: Continuous fiber reinforcement in 3D printed parts
**Biomimetic and Bio-Inspired Materials**:
Learning from nature for innovative solutions:
- **Self-healing materials**: Inspired by biological healing mechanisms
- **Adaptive structures**: Variable properties responding to environment
- **Hierarchical materials**: Multi-scale structures for optimized performance
- **Sustainable processing**: Bio-inspired manufacturing methods
### **Digital Material Development**
**Digital Twins for Materials**:
Real-time monitoring and prediction of material behavior:
- **Embedded sensors**: Monitor stress, strain, temperature, chemical exposure
- **Predictive maintenance**: Anticipate failure before it occurs
- **Performance optimization**: Adjust operating conditions based on material state
- **Life extension strategies**: Optimize usage patterns for maximum service life
**Virtual Material Testing**:
Simulation reduces physical testing requirements:
- **Multi-scale modeling**: From atomic to continuum scale behavior
- **Accelerated aging simulation**: Predict long-term behavior quickly
- **Virtual certification**: Reduce testing costs for regulatory approval
- **Design space exploration**: Rapidly evaluate material alternatives
## Implementation Excellence: Best Practices
### **Organizational Capabilities Development**
**Material Selection Competency Building**:
Develop systematic organizational capabilities:
- **Knowledge management systems**: Capture and share material selection experience
- **Decision support tools**: Standardized methodologies and databases
- **Cross-functional collaboration**: Integrate design, manufacturing, and supply chain perspectives
- **Continuous learning programs**: Stay current with material technology advances
**Risk Management Framework**:
Systematic approach to material-related risks:
- **Supply chain risk assessment**: Single-source dependencies, geopolitical factors
- **Technology risk evaluation**: Maturity of new materials and processes
- **Performance risk mitigation**: Adequate testing and validation procedures
- **Economic risk management**: Cost volatility, currency fluctuations
### **Quality Assurance and Validation**
**Material Qualification Procedures**:
Ensure materials meet requirements in practice:
- **Incoming inspection protocols**: Verify material properties and certificates
- **Process qualification**: Validate manufacturing parameter effects
- **Statistical quality control**: Monitor property variations and trends
- **Traceability systems**: Track material lots through production and service
**Performance Validation Methods**:
Confirm material selection through testing:
- **Accelerated testing**: Predict long-term behavior in compressed time
- **Service condition simulation**: Replicate actual operating environment
- **Failure analysis procedures**: Learn from any material-related failures
- **Continuous monitoring**: Track in-service performance for validation
## Conclusion: Mastering Strategic Material Selection
Material selection mastery requires integrating deep technical knowledge with strategic business thinking and systematic decision-making processes. Success comes from understanding not just material properties, but how those properties translate into real-world performance, cost-effectiveness, and sustainability outcomes.
The most successful engineers develop comprehensive frameworks that consider all stakeholders and lifecycle phases while remaining flexible enough to adapt to new technologies and changing requirements. This systematic approach, combined with continuous learning and strong supplier relationships, enables consistently excellent material selection decisions.
As materials technology continues advancing rapidly, the engineers who master these strategic selection principles while staying current with emerging technologies will create innovative solutions that provide lasting competitive advantages. The key is balancing technical excellence with business acumen and sustainability consciousness.
**What material selection challenges are you facing in your current projects? I'd welcome the opportunity to discuss specific applications and share additional insights from my experience across diverse industries.**
---
*Interested in exploring more engineering insights? Check out my articles on [Advanced CAD Technologies](/blog/mastering-cad-technology-mechanical-design) and [Sustainable Engineering Practices](/blog/sustainable-engineering-practices), or view my [portfolio of innovative engineering solutions](/portfolio) demonstrating these material selection principles in action.*
About the Author
Related Articles
You Might Also Like
Continue exploring with these hand-picked articles related to your interests.
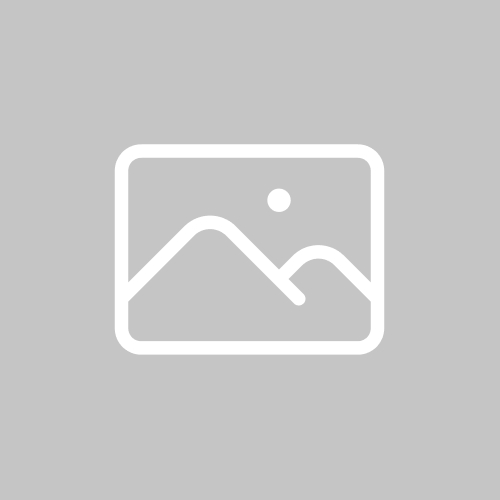
8 min read
The Future of Mechanical Engineering in Sustainable Design
Exploring how mechanical engineers are leading the transformation toward sustainable solutions while maintaining performance excellence and driving innovation in design practices.
Sustainable EngineeringGreen DesignClimate Solutions +2

8 min read
Mastering CAD Technology: Advanced Techniques for Modern Mechanical Design
A comprehensive exploration of cutting-edge CAD technologies, advanced automation techniques, and AI-powered design methodologies that are revolutionizing mechanical engineering workflows and productivity.
CADSolidWorksCATIA +5
Looking for more insights?