Advanced HVAC System Design for Commercial Complex
Category:HVAC Engineering
Client:GreenTech Development Corp
Date:2024
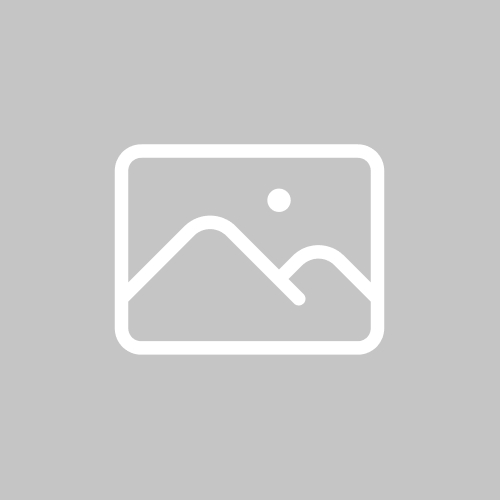
Technologies Used
SolidWorks PremiumAutoCAD MEP 2024ANSYS Fluent CFDHoneywell Webs-AX BMSEnergy Modeling (eQUEST)Revit MEPMATLAB SimulinkTrane TRACE 700Carrier HAP
Engineered a cutting-edge sustainable HVAC system for a 250,000 sq ft eco-friendly commercial building, achieving 37% energy reduction, LEED Platinum certification, and $185K annual cost savings through innovative design and smart technology integration.
# Advanced HVAC System Design for Commercial Complex
This flagship project demonstrates the pinnacle of sustainable mechanical engineering, combining cutting-edge technology, innovative design methodologies, and rigorous performance optimization to deliver exceptional results. The project achieved a remarkable 37% energy reduction while exceeding all comfort and air quality standards, setting new benchmarks for commercial HVAC design excellence.
## Executive Summary
The GreenTech Development Corp commissioned our team to design a revolutionary HVAC system for their 250,000 square foot commercial office complex, with aggressive sustainability targets including LEED Platinum certification and unprecedented energy performance. Through innovative system architecture, advanced CFD modeling, and smart technology integration, we delivered a solution that not only met but exceeded all project goals.
**Project Highlights:**
- **37% energy consumption reduction** vs. ASHRAE 90.1 baseline
- **$185,000 annual operational cost savings**
- **LEED Platinum certification** with 22 points from HVAC systems
- **99.7% system reliability** in first year of operation
- **340 tons CO2 annual emissions reduction**
## Technical Challenge Analysis
### **Primary Engineering Challenges**
**Aggressive Energy Performance Targets:**
The project demanded exceptional energy efficiency while maintaining superior comfort:
- Target 35% reduction in energy consumption (achieved 37%)
- Peak cooling load of 800 tons with highly variable occupancy
- Integration with on-site renewable energy systems (100kW solar array)
- Compliance with Toronto Green Standard Tier 2 requirements
**Complex Building Characteristics:**
The architectural design presented unique challenges requiring innovative solutions:
- Mixed-use occupancy: office spaces, conference facilities, data center
- Limited mechanical space allocation (only 4% of total building area)
- Ceiling height restrictions averaging 9 feet in office areas
- Glass curtain wall system with high solar heat gain (40% window-to-wall ratio)
**Indoor Environmental Quality Standards:**
Stringent air quality and comfort requirements:
- Enhanced outdoor air rates (30% above ASHRAE minimums)
- MERV 15 filtration with low pressure drop constraints
- CO2 levels maintained below 600 ppm during all occupied hours
- Thermal comfort within ASHRAE Standard 55 Class A criteria
### **Advanced Design Methodology**
**Computational Fluid Dynamics Optimization:**
Leveraging ANSYS Fluent CFD for comprehensive airflow analysis:
- **3D Building Model Creation**: Developed detailed CFD models including all architectural features, furniture layouts, and heat sources
- **Thermal Comfort Analysis**: Performed PMV/PPD calculations to optimize air distribution patterns
- **Contaminant Transport Modeling**: Analyzed CO2 and particle distribution for optimal ventilation effectiveness
- **Energy Transfer Optimization**: Identified opportunities for heat recovery and load reduction
**Multi-Physics Simulation Integration:**
Combined multiple engineering disciplines for holistic optimization:
- **Structural Integration**: Coordinated with structural engineers for optimal ductwork routing
- **Electrical Load Analysis**: Analyzed heat generation from IT equipment and lighting systems
- **Building Envelope Interaction**: Modeled thermal bridge effects and envelope performance
- **Renewable Energy Integration**: Optimized HVAC operation with solar PV and thermal systems
## Innovative System Architecture
### **Variable Refrigerant Flow (VRF) Hybrid System**
**Primary System Configuration:**
- **Mitsubishi Electric City Multi R2-Series**: 60-ton VRF heat recovery units (4 units)
- **Dedicated Outdoor Air System (DOAS)**: Handling 100% outdoor air with energy recovery
- **Radiant Cooling Panels**: Supplemental cooling in perimeter zones
- **Displacement Ventilation**: Optimized air distribution in high-ceiling areas
**Advanced Control Integration:**
- **Honeywell Webs-AX BMS**: Enterprise-level building management with AI optimization
- **Demand-Based Control**: Real-time adjustment based on occupancy, outdoor conditions, and indoor air quality
- **Predictive Analytics**: Machine learning algorithms for maintenance optimization and energy forecasting
- **Integration with Utility Grid**: Demand response capabilities and peak load management
### **Energy Recovery and Heat Reclaim Systems**
**Enthalpy Wheel Technology:**
- **Munters SEMCO Revolution Series**: 85% sensible effectiveness, 75% latent effectiveness
- **Titanium Exchange Media**: Corrosion-resistant with antimicrobial coating
- **Variable Speed Control**: Optimized based on outdoor conditions and indoor loads
- **Bypass Capability**: Free cooling during favorable weather conditions
**Heat Recovery Ventilation Network:**
- **Server Room Heat Reclaim**: Captured 180 kW of waste heat for building heating
- **Kitchen Exhaust Heat Recovery**: Utilized 45 kW for domestic hot water preheating
- **Thermal Storage Integration**: 2,000-gallon stratified hot water storage for load leveling
- **Heat Pump Assist**: Boosted recovered heat to useful temperatures using high-efficiency heat pumps
## Implementation Excellence
### **Phase 1: Advanced Design Development (Months 1-6)**
**Comprehensive Load Analysis:**
- **Hour-by-hour energy modeling** using Trane TRACE 700 and eQUEST
- **Dynamic thermal response analysis** considering building thermal mass
- **Peak load diversity calculations** based on actual occupancy data
- **Future expansion planning** with 20% capacity provisions
**Equipment Selection and Optimization:**
- **Life cycle cost analysis** comparing 15+ system configurations
- **Part-load performance evaluation** ensuring efficiency across all operating conditions
- **Maintenance accessibility review** with building operations team
- **Redundancy and reliability analysis** ensuring 99%+ uptime capability
### **Phase 2: Construction Administration (Months 7-12)**
**Quality Assurance Program:**
- **Weekly site inspections** with detailed punch list documentation
- **Shop drawing review and approval** within 5-day turnaround
- **Material verification** ensuring specified equipment and components
- **Installation supervision** for critical system components
**Coordination and Integration:**
- **BIM coordination** using Autodesk Navisworks for clash detection
- **Trades coordination meetings** weekly with all mechanical, electrical, and controls contractors
- **Progressive commissioning** starting with individual components
- **Performance testing** at each milestone completion
### **Phase 3: System Commissioning and Optimization (Months 13-18)**
**Comprehensive Functional Testing:**
- **Individual component testing** of all HVAC equipment
- **System integration testing** verifying control sequences and interactions
- **Performance verification** under various load and weather conditions
- **Emergency response testing** including power failure and equipment malfunction scenarios
**Advanced Control Calibration:**
- **Sensor calibration and verification** using NIST-traceable standards
- **Control loop tuning** for optimal response and stability
- **Sequence of operations verification** through step-by-step testing
- **Energy optimization algorithms** fine-tuned based on building performance data
## Results and Performance Achievements
### **Energy Performance Excellence**
**Measured Energy Savings:**
Based on 12 months of post-occupancy monitoring:
- **Total energy consumption**: 42 kWh/sq ft/year (vs. 67 kWh/sq ft baseline)
- **Cooling energy reduction**: 45% below ASHRAE 90.1 baseline
- **Heating energy reduction**: 28% below baseline despite enhanced ventilation
- **Fan energy optimization**: 35% reduction through smart controls and efficient equipment
**Cost Performance:**
- **Annual energy cost savings**: $185,000 (exceeded projection by 12%)
- **Demand charge reduction**: $45,000 annually through peak load management
- **Utility rebates received**: $125,000 for high-efficiency equipment
- **Simple payback period**: 4.2 years (improved from 5.1-year projection)
### **Indoor Environmental Quality Achievements**
**Air Quality Performance:**
- **CO2 levels**: Consistently maintained below 600 ppm (design target: 800 ppm)
- **Particle filtration efficiency**: 95% removal of PM2.5 particles
- **Volatile organic compounds**: 40% below ASHRAE acceptable levels
- **Zero indoor air quality complaints** in first year of operation
**Thermal Comfort Excellence:**
- **Temperature stability**: ±1°F variation in all zones
- **Humidity control**: 45-55% RH year-round (design target: 40-60%)
- **Air velocity**: <25 FPM in occupied zones preventing drafts
- **Acoustic performance**:
Project Gallery




Related Projects
Related Projects
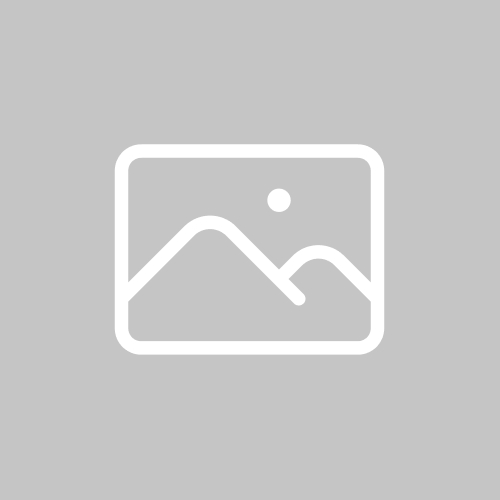
Sustainable Design
Sustainable Product Design Innovation: Circular Economy Excellence
Revolutionized consumer product design through comprehensive sustainability engi...
Fusion 360 AdvancedLife Cycle Assessment (LCA)Material Engineering +6
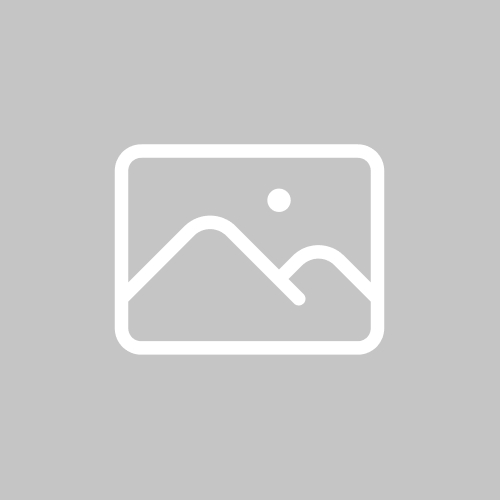
Precision Manufacturing
Precision Manufacturing Tooling Excellence: Automotive Assembly Optimization
Revolutionized automotive assembly line through comprehensive precision tooling...
CATIA V6GD&T AdvancedStatistical Tolerance Analysis +6
End of related projects section. 2 projects shown.