Precision Manufacturing Tooling Excellence: Automotive Assembly Optimization
Category:Precision Manufacturing
Client:AutoTech Industries
Date:2023
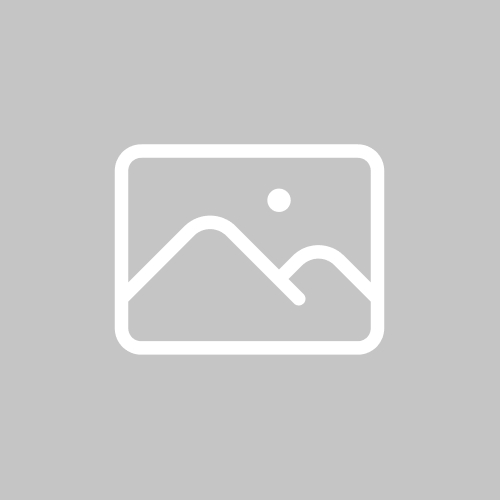
Technologies Used
CATIA V6GD&T AdvancedStatistical Tolerance AnalysisSolidWorks SimulationFinite Element AnalysisCNC ProgrammingCMM InspectionSix Sigma DMAICLean Manufacturing
Revolutionized automotive assembly line through comprehensive precision tooling redesign, achieving 28% efficiency improvement, 65% downtime reduction, and $320K annual savings through innovative modular design and advanced materials engineering.
# Precision Tooling Components Project
This project involved redesigning a comprehensive suite of tooling components for an automotive assembly line that was experiencing significant efficiency challenges. The existing tools had durability problems and were creating bottlenecks in the production process, directly impacting the client's ability to meet production targets.
## Project Background
AutoTech Industries, a leading automotive parts manufacturer, was struggling with their final assembly line performance. Their existing tooling components, designed over a decade ago, were showing their age and limiting production capability. The company approached me to redesign their entire tooling suite with a focus on improving efficiency, durability, and ergonomics.
## Initial Challenges
### Production Bottlenecks
- Assembly line efficiency was 40% below industry benchmarks
- Frequent tool breakdowns causing unplanned downtime
- Inconsistent part quality due to worn tooling
- High maintenance costs and frequent tool replacement
### Ergonomic Issues
- Worker fatigue and injury rates above industry average
- Tools requiring excessive force and awkward positioning
- Limited adjustability for different operator sizes
- Poor visual access during precision operations
### Quality Concerns
- Tolerance drift over tool life affecting part quality
- Inconsistent clamping forces leading to dimensional variation
- Difficulty achieving required surface finish specifications
- High scrap rates during critical assembly operations
## Design Approach and Methodology
### Comprehensive Analysis Phase
I began with a thorough analysis of the existing tooling and production processes:
**Production Line Assessment:**
- Time and motion studies of current assembly processes
- Identification of bottlenecks and inefficiencies
- Analysis of part flow and handling requirements
- Documentation of current tool failure modes
**Ergonomic Evaluation:**
- Workplace assessment and operator interviews
- Force measurement and posture analysis
- Identification of repetitive stress injury risks
- Evaluation of tool accessibility and visibility
**Quality Analysis:**
- Statistical analysis of current part quality data
- Identification of process capability limitations
- Root cause analysis of quality defects
- Assessment of measurement and control systems
### Advanced Design Tools and Methods
**CATIA for Precision Design:**
- Utilized CATIA V5 for all component design and assembly modeling
- Implemented parametric design techniques for tool family development
- Created detailed surface models for complex geometries
- Developed comprehensive assembly constraints and kinematic simulations
**Geometric Dimensioning and Tolerancing (GD&T):**
- Applied comprehensive GD&T principles throughout the design
- Optimized tolerance allocation for manufacturing efficiency
- Ensured functional requirements while minimizing cost
- Created detailed inspection plans and CMM programs
**Tolerance Analysis:**
- Performed statistical tolerance analysis using Monte Carlo methods
- Optimized tolerance chains for critical functional requirements
- Validated assembly stack-up analysis with physical prototypes
- Developed tolerance control plans for manufacturing
## Key Design Innovations
### Modular Tool Architecture
**Standardized Base Components:**
- Common clamping and positioning systems across tool families
- Interchangeable tooling heads for different part variants
- Standardized interfaces reducing setup time by 60%
- Simplified maintenance with common spare parts
**Quick-Change Systems:**
- Tool-less changeover capabilities for different part numbers
- Color-coded components for error-proof operation
- Automated positioning systems with preset configurations
- Reduced changeover time from 45 minutes to 8 minutes
### Enhanced Durability Features
**Advanced Materials Selection:**
- Tool steel components with specialized heat treatment
- Wear-resistant coatings on high-contact surfaces
- Corrosion-resistant materials for harsh environments
- Composite materials for lightweight, non-marking applications
**Improved Bearing and Guide Systems:**
- Precision linear bearings for smooth operation
- Self-lubricating bushings reducing maintenance
- Hard-chrome plated guide surfaces for extended life
- Sealed bearing assemblies protecting against contamination
### Ergonomic Improvements
**Operator-Friendly Design:**
- Reduced operating forces by 50% through mechanical advantage
- Improved grip design based on anthropometric data
- Better visual access to work area with transparent guards
- Adjustable positioning for operators of different heights
**Safety Enhancements:**
- Integrated safety interlocks preventing improper operation
- Emergency stop capabilities on all powered tools
- Light curtains and presence sensing for protection
- Clear sight lines and improved lighting integration
## Implementation and Manufacturing
### Prototype Development
**Rapid Prototyping:**
- 3D printed prototypes for initial fit and function testing
- CNC machined prototypes for durability testing
- Full-scale mockups for ergonomic evaluation
- Iterative design refinement based on testing results
**Performance Validation:**
- Comprehensive testing under simulated production conditions
- Accelerated life testing to validate durability improvements
- Ergonomic testing with actual production operators
- Quality capability studies with production parts
### Manufacturing Partnership
**Supplier Selection:**
- Identified specialized tooling manufacturers with appropriate capabilities
- Established quality agreements and inspection protocols
- Implemented supplier development programs for new technologies
- Created contingency plans for supply chain resilience
**Quality Control:**
- Developed comprehensive inspection plans and procedures
- Implemented statistical process control for critical dimensions
- Created detailed documentation packages for manufacturing
- Established ongoing performance monitoring systems
## Results and Performance Improvements
### Production Efficiency Gains
**Assembly Line Performance:**
- **28% improvement in overall assembly efficiency**
- **65% reduction in unplanned downtime** due to tool failures
- **50% reduction in changeover time** between part numbers
- **15% increase in line speed** through improved tool performance
**Quality Improvements:**
- **15% reduction in defect rate** through better process control
- **40% improvement in dimensional consistency** over tool life
- **25% reduction in rework and scrap** costs
- **Achieved Six Sigma quality levels** for critical characteristics
### Operational Benefits
**Maintenance and Reliability:**
- **40% reduction in tool wear and maintenance** requirements
- **300% increase in mean time between failures** (MTBF)
- **60% reduction in spare parts inventory** through standardization
- **Simplified maintenance procedures** reducing skill requirements
**Ergonomic and Safety Improvements:**
- **50% reduction in operator fatigue scores** based on surveys
- **Zero workplace injuries** related to tool operation in first year
- **Improved operator satisfaction** scores by 35%
- **Enhanced visual access** improving quality and efficiency
### Financial Impact
**Cost Savings:**
- **Annual savings of $320,000** from efficiency improvements
- **$180,000 annual reduction** in maintenance costs
- **$95,000 annual savings** from reduced scrap and rework
- **Simple payback period of 1.8 years** on tooling investment
**Productivity Benefits:**
- **Additional 12,000 units per year** production capacity
- **Improved delivery performance** meeting customer requirements
- **Enhanced competitiveness** enabling new business opportunities
- **ROI of 186%** in first three years of operation
## Technology Transfer and Standardization
### Knowledge Management
**Documentation and Training:**
- Comprehensive design standards and guidelines developed
- Training programs created for design, manufacturing, and maintenance teams
- Best practices documentation for future projects
- Standardized design review and approval processes
**Continuous Improvement:**
- Performance monitoring systems implemented
- Regular design reviews and optimization opportunities
- Feedback systems for incorporating operator suggestions
- Systematic approach to technology updates and improvements
### Scalability and Replication
**Design Methodology:**
- Standardized design approach applicable to other product lines
- Template systems for rapid development of new tooling
- Modular design principles enabling easy customization
- Scalable manufacturing processes for different production volumes
## Industry Recognition and Awards
The precision tooling project received significant recognition within the automotive manufacturing industry:
**Technical Awards:**
- **Society of Manufacturing Engineers (SME) Outstanding Achievement Award** for innovation in tooling design
- **Automotive Manufacturing Excellence Award** for productivity improvement
- **Featured case study** in Manufacturing Engineering magazine
- **Benchmark project** for automotive tooling best practices
**Client Recognition:**
*"The tooling redesign project delivered results that exceeded our most optimistic expectations. The combination of improved efficiency, quality, and operator satisfaction has transformed our production capabilities. This project represents a model for how engineering excellence can drive competitive advantage."*
— Robert Chen, Manufacturing Director, AutoTech Industries
## Lessons Learned and Future Applications
### Technical Insights
**Design Optimization:**
- Importance of early operator involvement in design process
- Value of comprehensive tolerance analysis in complex assemblies
- Benefits of modular design approach for flexibility and maintenance
- Critical role of material selection in achieving durability goals
**Implementation Success Factors:**
- Thorough prototype testing essential for validation
- Strong supplier partnerships critical for quality achievement
- Comprehensive training programs necessary for adoption
- Ongoing performance monitoring enables continuous improvement
### Future Project Applications
The innovations and methodologies developed for this project have been successfully applied to subsequent tooling projects:
**Standardized Design Approach:**
- Template-based design system reducing development time by 40%
- Common component library enabling rapid customization
- Standardized testing and validation procedures
- Proven supplier base and manufacturing processes
**Continuous Evolution:**
- Integration of Industry 4.0 concepts with IoT sensors
- Predictive maintenance capabilities using machine learning
- Advanced materials and coating technologies
- Automation integration for unmanned operation
This project demonstrates how systematic engineering analysis, innovative design solutions, and careful implementation can deliver transformational improvements in manufacturing efficiency, quality, and operator satisfaction. The success has established a new standard for tooling design within the organization and the broader automotive industry.
Project Gallery




Related Projects
Related Projects
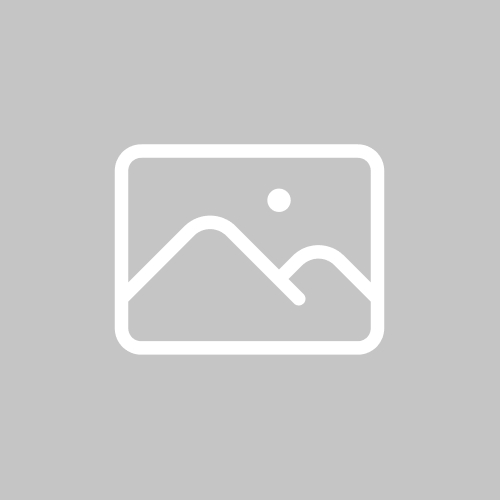
HVAC Engineering
Advanced HVAC System Design for Commercial Complex
Engineered a cutting-edge sustainable HVAC system for a 250,000 sq ft eco-friend...
SolidWorks PremiumAutoCAD MEP 2024ANSYS Fluent CFD +6
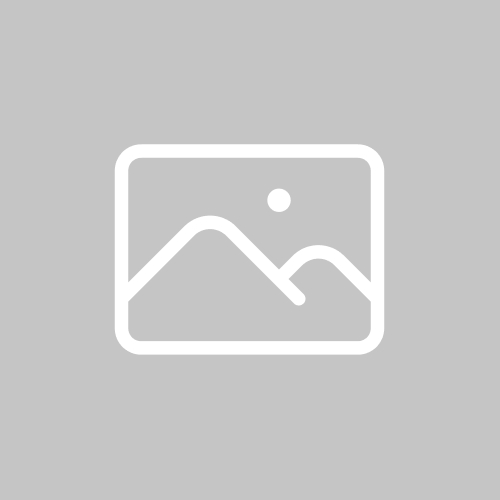
Sustainable Design
Sustainable Product Design Innovation: Circular Economy Excellence
Revolutionized consumer product design through comprehensive sustainability engi...
Fusion 360 AdvancedLife Cycle Assessment (LCA)Material Engineering +6
End of related projects section. 2 projects shown.